When we attend a conference, one of the most common interactions we have is: “I’ve been a customer for a long time. So… got anything new I should know about?”
The fact of the matter is we are always working on multiple improvement projects. However, some may be obvious to customers and some may not.
Internal self improvement projects
Not obvious but important self-improvement projects include:
- Computer virus training – Keeping your data safe.
- Job cross training – Allowing us to get the work done even when someone is sick or getting a little rest and relaxation.
- Fire extinguisher training – Just in case there is a fire, keeping the place open for business.
- Vendor evaluations – Making sure our costs remain in control.
- Lab method improvements
- Integrity and Ethics training – Imagine every result is measuring your Mom’s safety
- Reduce background on the ethylene oxide media – It’s beautiful now.
While these valuable projects reduce costs, reduce risk, and make the lab run more efficiently, they are not exactly what customers mean when they ask, “what’s new”.
So, what is new?
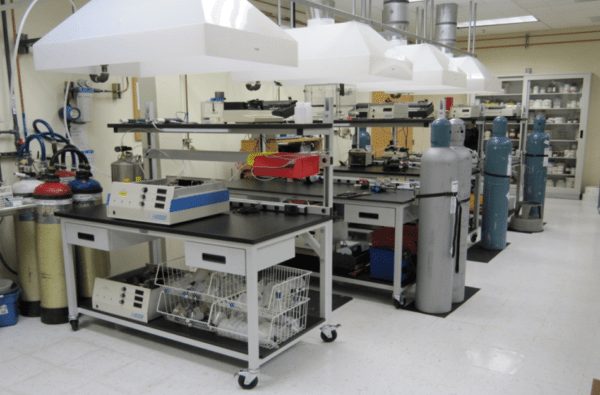
The Recently Completed
- The new carbon. The flexible charcoal inside many of our badges is not easy to make. When we bought the TraceAir badge, we switched over to the PTFE/Charcoal that we still use today. However, back then, there was only one viable vendor that could make it. In fact, every company we asked told us the PTFE/Charcoal mixture was impossible. The ratio of PTFE to charcoal was just too high. This made us nervous, which is one reason why when we ordered, we ordered 10 to 15 years worth. In the meantime, we continued our quest to find another vendor. Unfortunately, before we found one, a few years ago, our charcoal vendor announced they would no longer make any more. They even refused to give us an outline of the process. Yes, those were exciting times indeed. Fortunately, a resource was found and we were able to make our own media. And we are rolling now. We have total control over the process. Batch after batch, like the one before. A tremendous improvement.
- The new website.
- Dynamic sampling guide.
- Works on all devices.
- Helpful videos and blogs.
- Use the search engine and you’ll find it.
- If you are a laboratory, we have a page just for you. Got the resources for labs page.
- More published validations than ever before.
- Still can not find what you need? Try the Online chat. Talk to someone right online whenever you have a question. If were aren’t available, leave an email and we will get back to you right away.
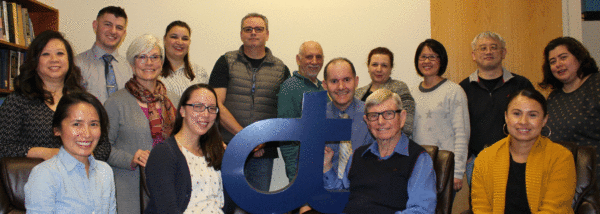
On the horizon
- Our own Hydrogen Peroxide badges
- After years of reselling another hydrogen peroxide badge, we are in the final validation steps. It took some effort to solve a stability issue and we will need to get the analysis added to our accreditation, but the major challenges have been solved.
- Ammonia by IC
- We have an Ammonia badge. There are two areas we would like to improve with the current method. 1) Any amine will interfere and cause a positive bias. While it is very unlikely for someone to have both Ammonia and other amines in the same environment, it would be an improvement to use a method that greatly reduces that possibility. 2) The method isn’t sensitive enough for STEL monitoring. However, with an ion chromatograph in cation mode, the reporting limit will be low enough to use our 584 badge for STEL.
- Acrolein
- The Acrolein badge (592) is for 8 hour monitoring only. Even at 8 hours, the reporting limit is very close to the OSHA PEL. We would like a reporting limit for an 8 hour exposure to be 5 to 10 times below the PEL. Currently it is only 1/2 the PEL. There are at least two ways to lower the acrolein badge reporting limit on a badge.:
- Improve the reporting limit of the existing method by using a splitless injection. (We are currently verifying we can regularly see a lower reporting limit.)
- Change the badge to the 571 badge. The 571 will collect Acrolein and the method should be 5 to 10 times more sensitive. However there is a technical issue that must be overcome or the results will be biased low. This is the preferred improvement because it would make the 592 badge unnecessary.
- The Acrolein badge (592) is for 8 hour monitoring only. Even at 8 hours, the reporting limit is very close to the OSHA PEL. We would like a reporting limit for an 8 hour exposure to be 5 to 10 times below the PEL. Currently it is only 1/2 the PEL. There are at least two ways to lower the acrolein badge reporting limit on a badge.:
There is more, but… I can’t tell you everything. Continuous improvement may be a cliché , but it is absolutely necessary to keep a business successful. Every day I arrive at work, I am focused on making the business better than it was the day before.