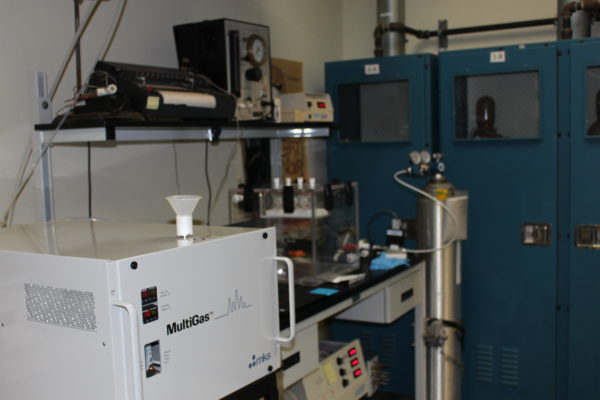
Authored by Maria Peralta PhD.
Our Miller-Nelson lab in Livermore specializes in generating chemical vapors for testing of media designed to remove chemical contaminants. Our customers specify concentration, flow, humidity, and temperature and we take care of the testing. But how do we know we are testing at the challenge concentration we really want? Buck calibrators and flow meters verify our flow; humidity and temperature probes can easily monitor relative humidity and temperature in real time, but what can we use to measure high concentration hazardous gases? This is where our newly acquired fourier transform infrared gas analyzer shines.
It is essential for us to try and verify the vapor generation concentration of challenge agents to ensure we are providing accurate testing conditions to all our customers, no matter the type of testing. Because of this, we continuously strive to offer the most accurate experimental set-up and detection methods possible. Challenge concentrations are orders of magnitude above the PEL, like hydrogen fluoride (HF) at 70 ppm, formaldehyde (HCHO) at 500 ppm or phosgene (COCl2) at 250 ppm. Measuring these high concentrations using existing OSHA and NIOSH method is impractical because they are designed to detect at levels near the PEL, leaving the challenge concentration range well outside the capability of the methods.
To validate the challenge gas concentration, we need to measure the gas levels in situ using a method that features a stable calibration over a wide dynamic range. The FTIR gas analyzer we have added to our Miller-Nelson lab, the MKS MultiGas 2030 FT-IR is capable of doing just this with its internal library of hundreds of calibrations for low detection limits, near PEL and high concentration ranges. We can use the FTIR for both challenge concentration validation and breakthrough detection. Below are a few examples where we have been able to validate the generation of challenge concentrations of hazardous gasses commonly tested in our lab.
Using Dilute Gas for Generation

Most of our standard challenge tests utilize a pressurized cylinder of dilute gas as the source for the challenge agent. Using the certified gas concentration of the dilute cylinder, we can calculate the flow needed from the cylinder to mix with the conditioned atmosphere for the desired test concentration. Two examples highlighted here are nitrogen dioxide (NO2) and phosgene (COCl2). NO2 is considered a “semi-difficult” gas due to its decomposition into nitric oxide (NO) and oxygen (O2) over time. Because of this issue, it becomes even more important to validate the concentration of the NO2 challenge and to ensure it has not decomposed. Below, in figure 1 and 2, you can see experimental values for generation of both NO2 and COCl2. The theoretical generation for NO2 was 200 ppm and 250 ppm for COCl2, both at 100 LPM. Over a ten-minute period, the average generation of NO2 was 202 ± 0.42 and 251 ± 0.82 ppm for COCl2, both within 5% of the mathematically derived generation. The background NO concentration was also detected and found to be low, approx. 4.3 ppm.
Using a Liquid Solution for Generation
Not all challenge agents are available in gas form, a significant amount originate as a liquid. For these tests, we use a specially built vaporizer allowing us to transform the liquid to the gaseous phase while passing conditioned air over the heating element, taking the newly transformed challenge agent into the air stream and onto the testing media. Theoretically, we can assume all of the liquid introduced into the vaporizer is converted but that can now be checked with the FTIR. Two examples highlighted here are carbon tetrachloride (CCl4) and formaldehyde (HCHO) in figures 3 and 4, respectively. For CCl4, the average generation was 1025 ± 18.7 when the theoretical generation was 1000 ppm, within 5 %. Experimental and theoretical generation for HCHO was 500 ppm, with the FTIR measuring a standard deviation of 9.
The four examples highlighted here show the accuracy of generation concentrations in the Miller-Nelson lab along with showcasing the ability of the FTIR to detect high concentrations of hazardous gases. We hope to continue to use the FTIR to further the capabilities of our respirator cartridge lab.